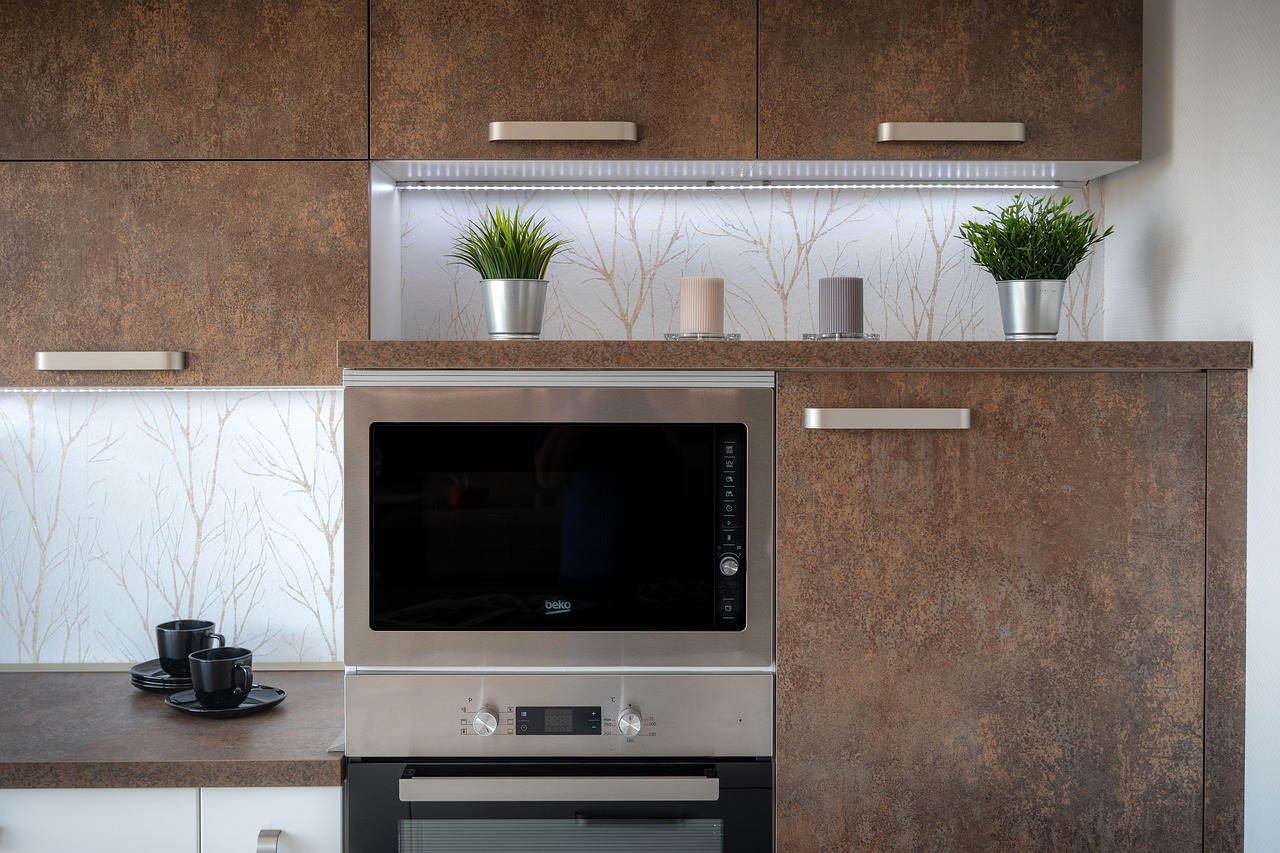
When it comes to energy efficiency, every detail matters, especially in high-heat environments like powder coating ovens. These machines run for extended periods, consuming significant amounts of energy. The good news? The right insulation can make all the difference. A powder coating oven with superior insulation is not just about maintaining heat but also about optimizing energy usage, reducing operational costs, and increasing productivity. Let’s dive into how better insulation can lead to a more energy-efficient system.
Minimizing Thermal Losses Through Enhanced Insulation Layers
A well-insulated powder coating oven is key to preventing heat from escaping into the surrounding environment. The less heat that escapes, the less energy is required to maintain the desired temperature inside the oven. This is where enhanced insulation layers come into play. By using modern materials that trap heat within the oven walls, manufacturers can significantly reduce thermal losses.
These insulation layers act like a shield, capturing the heat that would otherwise dissipate. As a result, the oven requires less frequent heating cycles, directly translating to lower energy consumption. Additionally, the reduced heat loss means that the workspace around the oven stays cooler, creating a more comfortable and safer environment for workers.
Retaining Consistent Internal Temperatures During Extended Operations
A critical factor in powder coating efficiency is the ability to maintain a consistent internal temperature, even during long operational hours. When the oven’s temperature fluctuates, energy is wasted as the heating system works harder to re-establish the set temperature. Superior insulation helps combat this issue by keeping the heat inside where it’s needed.
For large-scale operations where ovens run continuously, temperature consistency is essential to ensure even coating results and reduce energy waste. Superior insulation maintains these internal temperatures with minimal energy input, allowing for more predictable and uniform results across batches.
Optimizing Heat Reflection to Reduce Energy Consumption
A lesser-known aspect of energy efficiency in powder coating ovens is heat reflection. High-quality insulation materials often include reflective properties that bounce heat back into the oven chamber. This reduces the amount of energy required to maintain optimal temperatures, as more of the generated heat is effectively used.
By optimizing heat reflection, the oven can operate more efficiently, using less energy to maintain the same performance level. This feature is particularly useful in larger ovens that cover a greater surface area, where heat loss can otherwise become a significant issue.
Additionally, reflective insulation minimizes the need for the heating system to work overtime, which can help prolong the life of the oven. The more efficiently heat is used, the fewer power surges and interruptions the oven experiences, leading to smoother and more cost-effective operations.
Controlling External Heat Transfer for Better Resource Utilization
Powder coating ovens naturally generate a lot of heat, but not all of it needs to be wasted. Superior insulation also controls how much heat is transferred outside the oven, ensuring that external surfaces stay cool while the heat is retained inside. This control over heat transfer leads to better resource utilization, as energy isn’t wasted heating up areas outside the oven chamber.
This benefit goes beyond just energy efficiency. By limiting external heat transfer, you can also enhance workplace safety. Reduced external heat means workers are less likely to come into contact with dangerously hot surfaces, and overall environmental temperatures are easier to manage, especially in tight production spaces.
Stabilizing the Heating Cycle to Prevent Unnecessary Power Surges
One of the most energy-draining aspects of running a powder coating oven is dealing with power surges caused by inconsistent heating cycles. Without proper insulation, ovens experience rapid temperature drops, triggering heating elements to work harder and causing spikes in power usage. Superior insulation, however, stabilizes the heating cycle, preventing these sudden drops.
With a stable heating cycle, the oven requires less energy to maintain the set temperature, as it doesn’t have to compensate for frequent heat loss. This leads to smoother, more consistent energy usage, eliminating wasteful spikes that drive up utility bills.
Facilitating Faster Heat Recovery Times for Increased Efficiency
In any industrial setting, time is money, and faster heat recovery times translate directly into increased productivity. With superior insulation, powder coating ovens can recover heat much more quickly after opening the door or during cycle changes. This quicker recovery means less downtime and reduced energy consumption as the oven doesn’t have to work as hard to regain the ideal temperature.
When heat is retained efficiently, ovens can return to their operating temperatures faster, allowing for a more streamlined workflow. This also improves the overall efficiency of the coating process, ensuring that production schedules stay on track without excessive energy costs.
Faster heat recovery times also improve batch consistency, leading to fewer rejected items and less wasted material. The end result? A more energy-efficient operation with better product outcomes, which is essential for maintaining profitability in today’s competitive market.
Leave a Reply