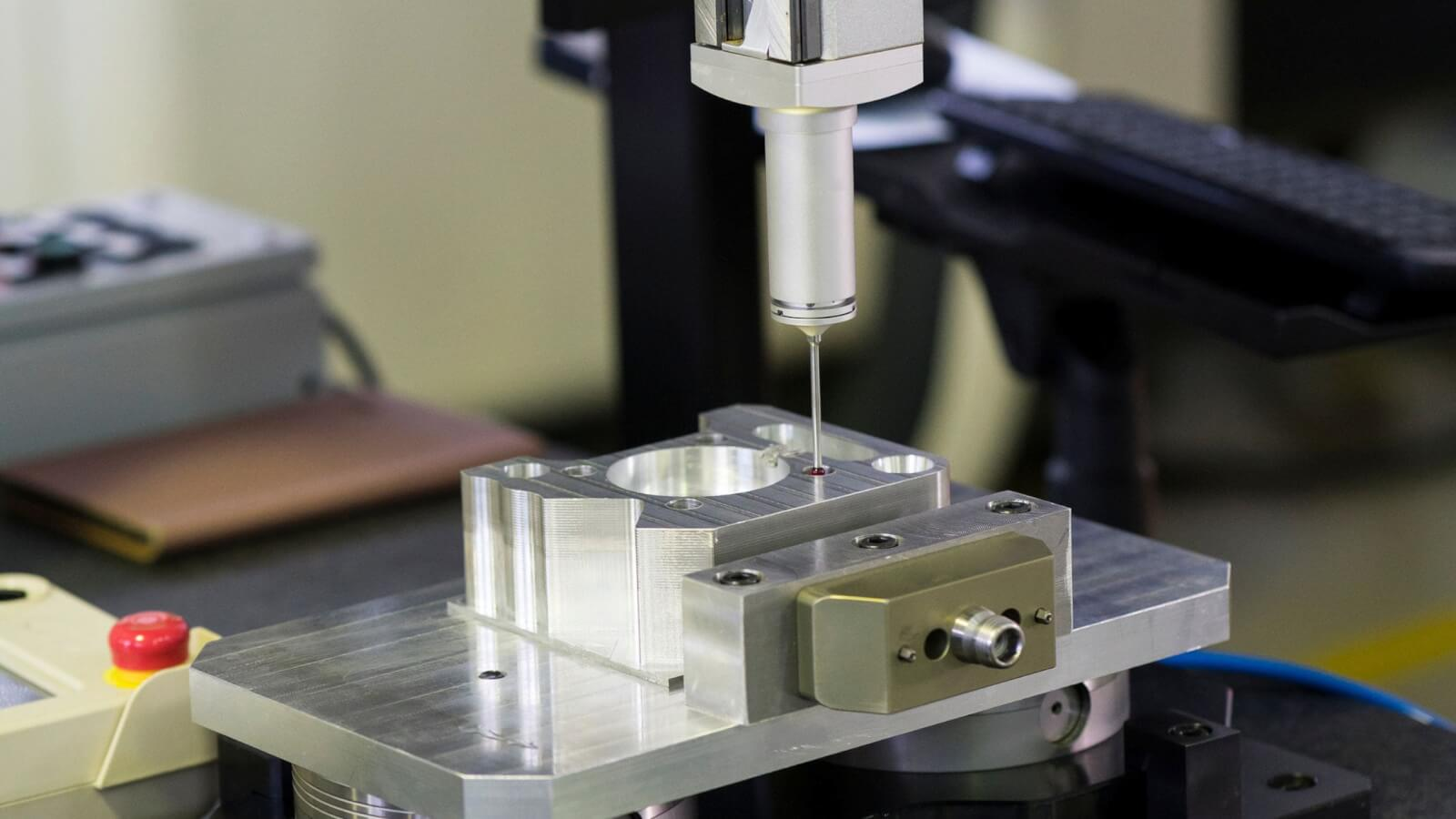
Controlling tolerances is essential in CNC milling. It plays a role in machined parts’ functionality, fit, and overall quality. To achieve the right tolerance, you need to combine some techniques. Some methods are precise machining practices, careful material selection, and strict quality control processes.
This article will examine key strategies to ensure tight tolerance control in CNC milled parts.
Understanding Machining Tolerance
Machining tolerances describe the acceptable range of variation in a part’s dimensions, shape, and position of the design parameters. These tolerances are vital since ultimate precision in manufacturing is unattainable. Tolerances guarantee that parts fit together correctly, work properly, and fulfill performance requirements. Tolerances are often defined as a range within which the part’s dimensions and features must fall. Precision is essential while milling using CNC machines. Adhering to tight tolerances and knowing machining tolerance charts are critical for making high-quality components. Properly specified tolerances in machine design and strict adherence to CNC tolerance requirements ensure that parts fit and work reliably. Close precision machining is essential for complex designs. However, conventional tolerances serve as a basis for typical manufacturing requirements.
Before Quotation for CNC Milled Parts
Below are the best practices to follow before quotation for CNC milled parts:
Find the Right Workshop
Choosing the correct workshop is the first step toward achieving perfection. The workshop’s location and structural environment can considerably impact machining precision. For example, workshops on the first floor (ground floor) are often preferred because higher floors can produce vibrations that interfere with precision machining.
These vibrations, generally more evident at higher levels, might interrupt the machining process, resulting in mistakes. Therefore, selecting a stable environment where precise CNC components may be produced without interference from external variables such as floor vibrations is critical.
Assess the Workshop’s Capabilities
Before starting with a quotation, evaluating the workshop’s capabilities is important. This includes assessing the range of CNC machines available, operator experience, and quality control procedures in place. A workplace with advanced machinery and competent workers is likelier to produce items with tight tolerances. In addition, enquire about the workshop’s experience with similar projects to be sure they have the necessary skills for your specific needs.
Verify Material Availability
Material availability is another important element to consider before requesting a quote. Check that the workshop can obtain the specific materials needed for your parts. If materials are not easily available, it may result in delays or quality sacrifices. Discussing material availability early on helps avoid potential problems later in manufacturing.
Understand Lead Times
The complexity of the parts, the availability of materials, and the workshop’s present demand can all substantially impact lead times. Before asking for a quote, you should know how long your project should take. This will support your planning and guarantee that the timelines you set for your projects are reasonable.
Clarify Tolerance Requirements
Specify the tolerance requirements for your CNC-milled items before getting a quotation. It’s crucial to let the workshop know what level of precision is needed for each element, as the requirements could vary. Giving clear tolerance criteria upfront guarantees that the workshop can evaluate your requirements accurately and deliver a competitive quote.
Consider Design for Manufacturability (DFM)
Before requesting a quote, having a Design for Manufacturability (DFM) conversation with the workshop may be helpful. DFM involves reviewing the part design to identify possible manufacturing issues and offer changes that could make manufacturing easier without sacrificing functionality. This cooperative approach can lead to shorter lead times, lower costs, and improved outcomes.
Review Quality Assurance Processes
Before accepting a quote, it is crucial to comprehend the workshop’s quality assurance (QA) procedures. Find out what standards, certifications, and inspection procedures the workshop uses to ensure the parts are within the required tolerances. A workshop with strong quality assurance procedures will deliver reliable, high-quality items.
Discuss Post-Processing Requirements
Before requesting a quote, discuss your components’ post-processing needs, like anodizing, heat treatment, or surface finishing. When getting a quote, it’s vital to consider these processes since they may impact the final dimensions and tolerances. Ensuring the CNC mill shop has trustworthy partners or can manage these procedures will be important to achieve the intended results.
During Quotation for CNC Milled Parts
Below are the best practices to follow during quotation for CNC milled parts:
Choice of Materials
Material choice plays a vital role in achieving desired tolerances. Different materials react differently during the machining process, influencing the ease with which tight tolerances can be maintained. For example, softer metals like aluminum are generally easier to machine to tight tolerances than harder metals like stainless steel. Additionally, consistent material quality is vital. Material composition or treatment variations can lead to discrepancies in the final part dimensions.
Manufacturing Methods
Another critical factor is selecting the appropriate manufacturing method. Depending on the part’s design, some methods may be more suitable for maintaining tight tolerances. For instance, CNC milling can achieve fine details and precise dimensions, but it requires careful consideration of the tool paths, cutting speeds, and feeds.
Surface Roughness Requirements
Surface finish requirements also need to be factored into the quotation process. Some applications demand smooth surfaces, which can be challenging without compromising dimensional accuracy. Discussing surface roughness requirements early on ensures that the machining process is designed to meet both the dimensional and finish criteria.
Application of the Product
Understanding the application of the CNC milled part helps set realistic tolerance expectations. Parts subjected to high loads or extreme conditions may require tighter tolerances to ensure longevity and performance. Therefore, it’s essential to communicate the intended use of the parts during the quotation phase.
Budget
Budget constraints may impact the tolerances that can be achieved. Tighter tolerances frequently necessitate more advanced machining techniques, higher-quality materials, and additional time, which can raise costs. To get the greatest results, it is important to strike a compromise between the demand for precision and budgetary constraints.
After Quotation for CNC Milled Parts
Below are the best practices to follow after quotation for CNC milled parts:
Use Quality CNC Machines
CNC machines’ precision directly impacts their ability to maintain tight tolerances. A machine with a tolerance of ±0.02 mm may struggle to achieve a tolerance of ±0.01 mm consistently. Thus, investing in high-quality machining centers is important. However, it is crucial to note that the most complicated devices are not usually the most accurate; thus, carefully considering individual requirements is essential.
Balance Tool Holder
Balanced tool holders are essential for maintaining precision in CNC machining. Unbalanced tool holders can produce vibrations, resulting in inaccuracies in the finished item. High-quality tool holders, such as those from MST or Haimer, are intended to reduce imbalance and can be adjusted for precision. Generally, a well-balanced tool holder should create less jitter, keeping the machining process stable and accurate.
Use Sharp Cutting Tool
The Sharpness of cutting tools considerably impacts the capacity to attain tight tolerances. Dull tools can cause poor cutting performance, increased machine wear, and inaccuracies in the finished product. On the other hand, Sharp tools allow for precision cutting while maintaining the part’s specified dimensions. Regular maintenance and good tool selection are essential to ensure cutting instruments remain effective.
Use Good Material Suppliers
The quality of materials used in CNC machining varies greatly, even within the same grade. It is critical to get products from reputable vendors who deliver consistent quality. Certifications can be useful in verifying material composition but do not necessarily ensure machining performance. Building partnerships with reliable suppliers via trial and error ensures that the materials are of good quality and suited for tight tolerances.
Deploy an On-Machine Inspection System
In-process inspection systems like Renishaw’s are crucial for maintaining tight milling tolerances. These systems use probes to measure part dimensions while the part remains on the machine, allowing for real-time modifications. On-machine inspection devices help to save costly rework by detecting deviations early and ensuring that parts satisfy the necessary tolerances.
Validation Process
A strong validation process is required to ensure strict tolerances are routinely met. This procedure incorporates regular inspections at various stages of production, statistical process control (SPC) methodologies, and careful documentation of measurement data. Collaboration between machinists and quality control staff is essential for developing a validation procedure that ensures the final parts meet or exceed the required tolerances.
Conclusion
Achieving tight tolerance control in CNC milled parts requires a comprehensive approach. This approach begins with the right workshop and continues through careful material selection, precision machining, and strict validation. By following these top practices, manufacturers can ensure that their CNC-milled parts meet the highest standards of accuracy and quality, leading to reliable and successful products.
Leave a Reply